Our Core Alloys And Their Applications
Specialists in high performance metal alloys for a wide variety of industries our core alloys have been used for numerous applications, many of which are explained below…
UNS S32760
From the Thames Barrier to subsea pipework systems UNS S32760 has been used for a wide range of applications because of its high impact strength, resistance to stress corrosion cracking and other characteristics. Also known as Zeron100® it’s incredibly versatile and has been used for the following applications:
Used to extend the lifespan of the Thames Barrier
Expected to last for over 60 years UNS S32760 was used to extend the lifespan of the Thames Barrier in Greenwich, London. Its high corrosion resistance in seawater and high hardness to resist wear made it extremely desirable.
#### **UNS S32760 For The Marine Industry**With a high alloy content UNS S32760 displays extreme corrosion resistance in both natural and treated seawater. Easy to work with its often used to create a range of products including vessels, piping and pumps.
### **Alloy 400**Well known for its corrosion resistance, weldability and ductility Alloy 400 is a super duplex stainless steel that performs excellently in seawater and other highly corrosive environments.
Incredibly versatile Alloy 400 was chosen to create pump components, brine heaters and salt production equipment. And because it can be used to handle sulphuric acid, fluorine, hydrofluoric acid and hydrogen fluoride it’s perfect for manufacturing corrosion resistant chemical processing equipment.
Other applications of alloy 400 include:
- Power plants
- Industrial heat exchangers
- Oil and gas applications
RA330®
Specifically created for the thermal process industries RA330® displays excellent strength at elevated temperatures, is resistant to thermal shock and is resistant to carburization, which is why it was selected for the following applications:
RA330 Tube Supports
A leading gulf coast petroleum refinery recently opted to use RA330® for tube supports in one of their direct-fired furnaces. The refinery opted for RA330® because previous cast supports failed due to the presence of casting voids which caused cracking.
#### **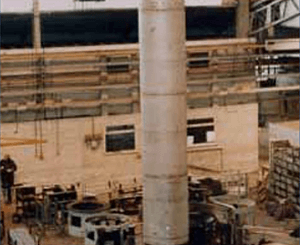RA330 Carburizing Retorts**Due to its excellent resistance to thermal shock and carburization RA330 was used to create a large carburizing retort. Unlike other materials previously used RA330 offers a high level, efficient performance.
#### **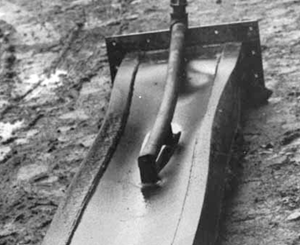RA330 Muffle Sintering Stage**RA330® was used to create a rectangular muffle for the sintering stage of a powdered metal application. The muffle, specifically used for sintering iron, needed to handle temperatures in excess of 1093.33°C with excursions up to 1121°C. After an impressive 17 months the RA330® muffle displayed no signs of damage or atmosphere leaks, lasting longer than any other muffle fitted to this specific furnace.
Alloy C276
Stack Liners, Ducts, Heat Exchangers and Evaporators have all been created using our core Alloy C276. Known as the most universally corrosion resistant material available today, it is used in a variety of environments from moderately oxidizing to strong reducing conditions. Industries that have turned to Alloy C276 include:
- Petrochemical and chemical processing
- Power generation
- Pharmaceutical
- Pulp and paper production
- Waste treatment
For more information on our core alloys on their applications feel free to contact us today and discuss your needs with one of our experts.