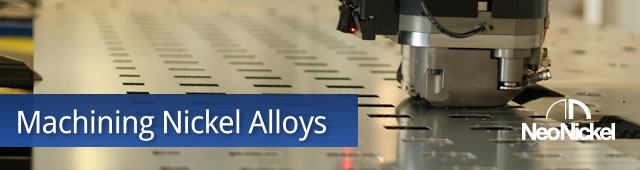
Nickel-based temperature and corrosion resisting alloys can be difficult to machine. They do harden rapidly and can weld to cutting tool surfaces; they also generate high heat levels when being cut, and thanks to their high shear strengths, offer a higher resistance to metal removal.
Why Do People Say Nickel is Hard to Machine?
Nickel is hard to machine when you don’t take the correct approach or use the right tools. machinists, managers, and process planners treat it like high strength, high resistance metal, which is a common mistake.
Although the physical properties are similar, when nickel is at the cutting edge, practice is different. Heat-treated metals (especially austenitic ones) have a higher tendency to chip under shear forces, which come from the tools used in machining.
Mid-range tools can work on some other high-strength metals, but nickel’s strength qualities mean there is no viable weak point, meaning only high-quality tools will suffice.
Some companies avoid nickel altogether, which means they end up with inferior alloys, is this you? It is possible to adapt to the specific manufacturing processes that nickel needs, so your applications no longer have to suffer.
However, these alloys offer many unique benefits in the processes where they are used and can be machined satisfactorily using conventional methods. So here are some general tips to guide you through these processes.
Nickel Machining Tips
### 1. Tooling Options When Machining Nickel Alloys
Thanks to the unique properties of the various nickel alloys, you will find that your tools may dull quite quickly. So it will be necessary to either re-sharpen tools or change tooling at regular intervals. It’s recommended that you use more expensive C grade inserts if these are available to you.
### 2. Drilling Factors
With CNC machines, if you are using insert drills, it’s best to select the same speeds (SFM) when facing, boring or turning any specific alloy. It’s also recommended that feed rates should be .002″ per revolution.
Cobalt drills should be your preferred option when using twist drill bits. Alternatively, high speed (HSS) drills should also work but usually at slower and steadier speeds. A final option, in specific applications, would be solid carbide drills.
### 3. Turning Points
If you are using steel cutting tools, speed as high as 35/FPM could likely be attained, with a feed of roughly .010″ to 0.12″ per revolution. When cutting off, you are likely to find that high-speed tools are more effective than carbide ones. Your tools should have a front clearance of around 7 degrees, and a tip larger than 25 degrees is suggested.
### 4. Reaming Actions
Here speeds should be half, and the feed around three times, your drill speed. Short tools are recommended with a marginal face rake of between 5 and 8 degrees.
### 5. Tapping Situations
It’s recommended that you choose a tap drill slightly larger than the standard drill recommendation for conventional threads. This is because the metal is likely to flow into the cut.
### 6. The Use of Coolants & Lubricants
Heat build-up is a significant cause of warpage. Aim to find what works best in your specific situation – often through a careful trial process. Here are a couple of suggestions to help. Firstly, in tapping and heavy drilling situations (involving large diameters or deep holes), a good choice is usually a light viscosity but heavy-duty petroleum cutting oil. For CNC equipment and engine lathes, you may find excellent results with water-miscible vegetable oil-based fluids.
### 7. Considering Capacity
A wide range of nickel alloys can be both bored and face-turned on almost any appropriate machine. You’ll consider specific factors such as cut-depth, speed, tooling and feed when making your individual choice. Both larger holes and tapping will require a high degree of machine power and strength.
### The Simplest Way to Obtain Expert Advice
The above is a general guide to the machining processes. Specific professional advice can easily be obtained from our experts. Contact us and tap into our thirty-plus years of experience in supplying high-performance nickel alloy solutions.